In the R&D project “Propeller Cupping”, the development of the new parametric SVA profile family laid the foundation for a standardised use of cup profiles in propeller design by extending the conventional geometry definition to include cup profiles up to supercavitating profiles.
In the project, this SVA profile family is to be made usable for propeller design for fast ships with large shaft inclination. Propellers with cup are to be critically analysed in order to find possibilities for improving the cavitation, erosion and operating behaviour. Essential parameters and the correct optimisation criteria for profile optimisation in propeller design must be worked out in order to achieve the objective of significantly improving the performance of the propeller at low cavitation numbers.
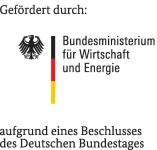
Title: | Propeller design method for low cavitation numbers |
Term: | 01/2021 – 06/2023 |
Project Manager: | Simon Froitzheim |
Founding: | Federal Ministry for Economic Affairs and Energy |
Project administration: | EuroNorm GmbH |
Reg.-No.: | 49MF200132 |
It must be possible to integrate the profile family into the optimisation process of propeller design programmes (lifting surface procedure VORTEX, optimiser VTXopt). The focus is on avoiding leading edge layer cavitation. The profile investigations are to be carried out both on the basis of a calculation method to be selected for thick profiles (e.g. XFOIL) and on the basis of CFD calculations. Based on the calculations, the calculation method for thick profiles will be validated and optimised for implementation in VTXopt. In addition, the calculations will be validated by means of experimental investigations.
Besides the mere suitability of cup propellers for modern fast ships, special attention is paid to the influence of the number of blades, as well as the way of scaling into the large version. The need for a dedicated friction line/correction method for cup propellers needs to be assessed and if needed, has to be developed.